Agility Helps Core Technology Thrive in the COVID-19 Market
By Louis Columbus, Enterprise Software Strategist | 06.18.20
How one supplier was able to meet spikes in demand as many employees worked from home.
The COVID-19 pandemic has pushed medical product manufacturers to rapidly scale up capacity while protecting the health of employees. One company that has successfully balanced these demands is Core Technology Molding Corporation. Leading firms, such as Merck, rely on the Greensboro, NC-based supplier to produce molded parts for biotechnology, medical technologies, and pharmaceuticals. And, the manufacturer now delivers products to 125 countries on five continents.
Prior to the pandemic, Core Technology had already established itself as a trusted provider to medical product companies with ISO-7 and ISO-6 certified medical clean rooms and a strong commitment to Six Sigma best practices. Then, early business continuity planning in February 2020, combined with agility made possible by the company’s DelmiaWorks manufacturing enterprise resource planning (ERP) system, enabled the company to meet dramatic spikes in demand even as many employees worked from home.
Competing on Quality and Trust
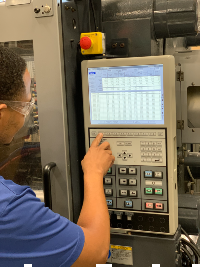
Constant feedback is an important aspect of a continuous improvement culture. Pictured above, the second shift process technician uses machine Integrated "Statistical Process Control" software. Image courtesy of Core Technology.
Core Technology specializes in the production of particularly small molded parts in direct patient use. Its highly automated assembly and finishing services follow certified production conditions according to cleanroom ISO Class 7, DIN EN ISO14644-1 for injection molding and ISO Class 6 for assembly. In this way, the manufacturer meets all of its customers’ requirements for stability, media resistance, and hygiene in every quantity. Moreover, investments in robotics have enabled the company to win deals against low-priced Chinese competitors who can’t offer the same quality or business continuity.
The company also takes a data-driven approach to its production strategies. Before starting Core Technology Molding, founder and CEO Geoff Foster was an industrial engineer and product manager at AMP Inc., Tyco Electronics, and Corning Life Sciences. This engineering background gave him an appreciation for implementing an ERP system that would facilitate data-driven decisions. The DelmiaWorks manufacturing ERP system now provides real-time monitoring that is integrated to quality, production scheduling, shipping and labeling, and traceability.
Additionally, Core Technology has established a strong foundation through its Six Sigma expertise, with more Six Sigma Black Belts on staff per capita than many comparably sized manufacturers.
"When our employees started getting Six Sigma training, black belt and green belt training, we were able to understand how all the data we collect comes together," observed Geoff Foster. "We're using advanced analytical techniques to understand and act on real-time process monitoring data, including overall equipment effectiveness, scrap rates, and production yield rates, among others."
Core Technology’s investments in employee expertise and ERP technology have enabled the manufacturer to meet the demands of its medical industry customers for real-time process monitoring of every supplier they source from—such as insights into the handling of production loads, quality levels, and machinery efficiency. The manufacturer’s pharmaceutical and medical device customers also perform periodic supplier audits onsite. The ability to run reports from the ERP system’s real-time process monitoring module helps Core technology prepare for these audits in just a few hours, and they can be done from anywhere there is an Internet connection.
Safely Meeting Demand During the Pandemic
In February 2020, the Core Technology executive team recognized that they needed to plan for the impact of COVID-19. Leading the business continuity planning were Geoff Foster and vice president of HR, environmental and safety Tonya Foster. Notably, as a registered nurse with a Bachelor of Science in Nursing (BSN) degree, Tonya Foster brought expertise in best practices for protecting employees from potential infection. The resulting plan addressed strategies for meeting Centers of Disease Control and Prevention (CDC) guidelines, scheduling employees and production runs to protect employees, and realigning production to support medical products in the highest demand, such as testing kits and personal protective equipment.
In executing on the business continuity plan, Core Technology has relied extensively on the technology and Six Sigma best practices that the manufacturer has put into place. For example, data-driven insights applied to Six Sigma have helped the company to improve production workloads, reduce the dependence on having too many workers on the production floor at once, and ensure that social distancing guidelines are met.
Additionally, with business continuity in mind, Core Technology manufacturing engineer and business development manager Brandon Frederick has implemented the ERP system with support for remote access. So, non-production employees are able to work safely from home, logging into the ERP system to get the real-time process monitoring data, analytics, and reports on which they rely. As a result, they can continue to provide the real-time information that pharmaceutical and medical device manufacturing customers require to ensure quality and on-time deliveries.
"Real-time data from our manufacturing ERP system enables us to be more proactive in protecting employees and helps us make better decisions about processes and equipment,” Geoff Foster observed. “We can also look at data from machine to machine, and determine which machine gives us the best results. Having that data is critical."
With its planning, processes, and technology in place, Core Technology has been able to run its Class 10,000 and Class 1000 medical clean rooms at capacity, providing the production availability to take on the rapid rise of orders from medical industry customers—while protecting the health and safety of employees.
Louis Columbus is currently serving as principal of DelmiaWorks (formerly IQMS). Previous positions include product management at Ingram Cloud, product marketing at iBASEt, Plex Systems, senior analyst at AMR Research (now Gartner), marketing and business development at Cincom Systems, Ingram Micro, a SaaS start-up and at hardware companies. Columbus is also a member of the Enterprise Irregulars. Professional experience includes marketing, product management, sales and industry analyst roles in the enterprise software and IT industries. Columbus’ academic background includes an MBA from Pepperdine University and completion of the Strategic Marketing Management and Digital Marketing Programs at the Stanford University Graduate School of Business. Louis teaches MBA courses in international business, global competitive strategies, international market research, and capstone courses in strategic planning and market research. Mr. Columbus has taught at California State University, Fullerton: University of California, Irvine; Marymount University, and Webster University. You can reach him on Twitter at @LouisColumbus.
Prior to the pandemic, Core Technology had already established itself as a trusted provider to medical product companies with ISO-7 and ISO-6 certified medical clean rooms and a strong commitment to Six Sigma best practices. Then, early business continuity planning in February 2020, combined with agility made possible by the company’s DelmiaWorks manufacturing enterprise resource planning (ERP) system, enabled the company to meet dramatic spikes in demand even as many employees worked from home.
Competing on Quality and Trust
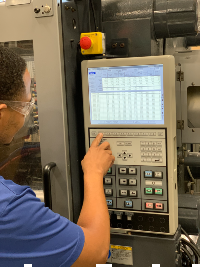
Constant feedback is an important aspect of a continuous improvement culture. Pictured above, the second shift process technician uses machine Integrated "Statistical Process Control" software. Image courtesy of Core Technology.
The company also takes a data-driven approach to its production strategies. Before starting Core Technology Molding, founder and CEO Geoff Foster was an industrial engineer and product manager at AMP Inc., Tyco Electronics, and Corning Life Sciences. This engineering background gave him an appreciation for implementing an ERP system that would facilitate data-driven decisions. The DelmiaWorks manufacturing ERP system now provides real-time monitoring that is integrated to quality, production scheduling, shipping and labeling, and traceability.
Additionally, Core Technology has established a strong foundation through its Six Sigma expertise, with more Six Sigma Black Belts on staff per capita than many comparably sized manufacturers.
"When our employees started getting Six Sigma training, black belt and green belt training, we were able to understand how all the data we collect comes together," observed Geoff Foster. "We're using advanced analytical techniques to understand and act on real-time process monitoring data, including overall equipment effectiveness, scrap rates, and production yield rates, among others."
Core Technology’s investments in employee expertise and ERP technology have enabled the manufacturer to meet the demands of its medical industry customers for real-time process monitoring of every supplier they source from—such as insights into the handling of production loads, quality levels, and machinery efficiency. The manufacturer’s pharmaceutical and medical device customers also perform periodic supplier audits onsite. The ability to run reports from the ERP system’s real-time process monitoring module helps Core technology prepare for these audits in just a few hours, and they can be done from anywhere there is an Internet connection.
Safely Meeting Demand During the Pandemic
In February 2020, the Core Technology executive team recognized that they needed to plan for the impact of COVID-19. Leading the business continuity planning were Geoff Foster and vice president of HR, environmental and safety Tonya Foster. Notably, as a registered nurse with a Bachelor of Science in Nursing (BSN) degree, Tonya Foster brought expertise in best practices for protecting employees from potential infection. The resulting plan addressed strategies for meeting Centers of Disease Control and Prevention (CDC) guidelines, scheduling employees and production runs to protect employees, and realigning production to support medical products in the highest demand, such as testing kits and personal protective equipment.
In executing on the business continuity plan, Core Technology has relied extensively on the technology and Six Sigma best practices that the manufacturer has put into place. For example, data-driven insights applied to Six Sigma have helped the company to improve production workloads, reduce the dependence on having too many workers on the production floor at once, and ensure that social distancing guidelines are met.
Additionally, with business continuity in mind, Core Technology manufacturing engineer and business development manager Brandon Frederick has implemented the ERP system with support for remote access. So, non-production employees are able to work safely from home, logging into the ERP system to get the real-time process monitoring data, analytics, and reports on which they rely. As a result, they can continue to provide the real-time information that pharmaceutical and medical device manufacturing customers require to ensure quality and on-time deliveries.
"Real-time data from our manufacturing ERP system enables us to be more proactive in protecting employees and helps us make better decisions about processes and equipment,” Geoff Foster observed. “We can also look at data from machine to machine, and determine which machine gives us the best results. Having that data is critical."
With its planning, processes, and technology in place, Core Technology has been able to run its Class 10,000 and Class 1000 medical clean rooms at capacity, providing the production availability to take on the rapid rise of orders from medical industry customers—while protecting the health and safety of employees.
Louis Columbus is currently serving as principal of DelmiaWorks (formerly IQMS). Previous positions include product management at Ingram Cloud, product marketing at iBASEt, Plex Systems, senior analyst at AMR Research (now Gartner), marketing and business development at Cincom Systems, Ingram Micro, a SaaS start-up and at hardware companies. Columbus is also a member of the Enterprise Irregulars. Professional experience includes marketing, product management, sales and industry analyst roles in the enterprise software and IT industries. Columbus’ academic background includes an MBA from Pepperdine University and completion of the Strategic Marketing Management and Digital Marketing Programs at the Stanford University Graduate School of Business. Louis teaches MBA courses in international business, global competitive strategies, international market research, and capstone courses in strategic planning and market research. Mr. Columbus has taught at California State University, Fullerton: University of California, Irvine; Marymount University, and Webster University. You can reach him on Twitter at @LouisColumbus.