Nathan Müller, EIT, Mechanical Engineer, StarFish Medical11.02.17
From silicones and epoxies to acrylic-based adhesives, the world of medical adhesives is broad in its choices and applications. As novel medical treatments and technologies have come forth, medical adhesives have flourished, integrating themselves into the designs of many medical devices. Components with materials that once provided difficulty—catheters, disposables, other compliant materials—are now reliably bonded in production lines with predictable and controlled medical adhesives. In this article, I’ll cover medical device adhesive specifications and failure modes, then outline the benefits of adhesives over fasteners, give insight into biocompatibility requirements, and offer some specific applications based on an adhesive’s type.
Specifications
To give a broad overview of medical device adhesives, the following table provides context to parameters and the corresponding performance of adhesives.
When choosing an adhesive, mechanical properties—along with chemical compatibility—are the fundamental factors to consider. Sound design practice, along with proper material and adhesive choices, will set the path towards successful design. Several failure modes and ways to circumvent them are outlined here in order to give clarity and lead to improved design using adhesives.
Failure Modes
In order to understand why adhesives fail, it is essential to acknowledge their mechanical modes of failure. There are three basic modes of failure, shown and explained below.
Adhesive failures are often due to a lack of surface preparation. This failure mode can be mitigated by several methods. Preparation of the substrate’s surface by using abrasives or bead/shot blasting to roughen will give better adhesion and bond strength. Cleanliness of the substrate is also of importance, due to the possibility of machining fluids, lubricants, and leftover materials (e.g., powder) causing adhesion issues. For most applications, degreasing with chemical methods—such as detergents and solvents—can lead to successful adhesion. For materials with lower surface energy, more specialized treatments (e.g., plasma or corona discharge) can enhance bondability.
Cohesive failure can be due to three key reasons. Higher thickness in bonds allows for more deformation in tension and shear, relying on the adhesives’ own strength between its internal bonds. As the thickness increases, the shear stresses increase, and therefore is more likely to lead to a cohesive failure. Mitigate this by following the adhesive’s directions closely, and by design of close fitting parts. Secondly, cohesive failure can be due insufficient bonding time or inadequate methods of curing (e.g., lack of full penetration of curing light). The final reason could simply be due to the maximum strength of the adhesive. Every adhesive will break at given stresses, and so careful planning for the application can allow for good results through a reliable bond. There are a number of factors that come together to create a properly cured adhesive. Following instructions from the adhesive’s manufacturer is key, as well as process control and verification testing, all of which can lead to consistent results for a bond.
Structural failure generally occurs due to stress concentrations created near a bonded joint. As with any material, there is an inherent yield and ultimate strength. Geometries and features of the component can amplify these effects, and lead to structural failure. Part analysis in software can reveal key flags during the design phase, leading to mitigations through design and allowing for an integral bond and part interface. In addition, chemical attack, particularly environmental stress cracking in plastics, can quickly cause structural failures in the base material.
Benefits of Adhesives over Fasteners
There are significant benefits of using adhesives over mechanical joining systems. This is dependent on the careful design and execution of the bonded joint. If well designed, adhesives can outshine mechanical bonding on several fronts.
Adhesives create a uniform and strong bond between materials by distributing stresses over an area. This reduces stress risers such as those that can occur with screws and rivets. Key to medical devices, adhesives do not require through holes, and can act simultaneously as both a sealant and a joining material. If an adhesive bond is designed as watertight, the area the adhesive covers will be protected from corrosion or liquid ingress. Space requirements are also an important consideration—adhesives can be used in place of fasteners when limited by the size of a joint or fastening region, as they are able to join materials with very limited additional volume. In some cases, a bonded assembly can be more durable than a fastened assembly due to vibration resistance, as adhesive will not loosen as with unsupported fasteners. Adhesives can save time and material cost during assembly, with the possibility of automation for high volumes. Automation, in certain cases, can be faster than with traditional fasteners, depending on the application. Also, depending on the adhesive selected, bonded assemblies can be disassembled through the application of adhesive removal compounds, allowing them to be disassembled alike to fastened assemblies.
Beyond function, the appearance of an assembly can be enhanced by adhesives, due to the absence of visible fasteners. From a risk mitigation standpoint, this also protects the user from device internals. Fasteners can be removed with tools, while most adhesives seal permanently and are arduous to separate.
Biocompatibility
A material is considered biocompatible if it lacks any negative interaction with living tissues or systems. Biocompatibility of a medical device that comes into human contact is of utmost importance, and should be top of mind during its development stage.
Merits of using adhesives over fasteners can also be applied to biocompatibility testing. By acting to seal parts together, adhesives limit the ingress of fluid into and between parts. This can reduce risk during testing due to less potential material contact (e.g., fluid contacts only external parts of device, thus excluding internals from the scope of biocompatibility testing).
As with all medical device testing, biocompatibility testing and validation is defined by the end use of the product and its component parts. The downselection for required testing involves defining a device category and the nature of bodily contact. Finally, the duration of contact defines further required testing. An important note is that the FDA only approves the final device, and not its component parts or materials. However, medical adhesive vendors can claim certain ISO 10993 or USP compliance by testing their cured adhesive, allowing designers to make the right adhesive choice for their device. These tests can clear a material for a particular application and provide confidence that the adhesive joints in an assembly will be non-toxic.
For further details on testing and requirements, consult biocompatibility standards ISO 10993 and USP series I to VI.
Applications
Adhesives can be categorized into the following segments:
Understanding the application for a given adhesive and the bond’s mechanical property requirements are crucial to bond joint design. So too are the adhesive types recommended for each application. The table below provides examples of typical materials and applications for a range of structural, non-structural, and pressure sensitive adhesives.
Conclusion
Medical devices require careful consideration when choosing adhesives. From design of the base part to the application method to the final intended use, many factors can affect the success of an adhesive joint. Prudent and conscious design choices are key factors in determining the success of any medical product.
Adhesives can offer many merits over designing with fasteners. They can provide cost reduction in many cases, and offer another choice to increase flexibility in design. They can be pre-tested by vendors to confirm their compliance with ISO 10993 or USP I to VI and be used to bond and seal between parts. These factors can assist in passing biocompatibility testing of the completed device. Overall, their applications are broad and their use in the medical field will only grow as both device variety and adhesive technologies advance in the years to come.
Nathan Müller, EIT, is a mechanical engineer at StarFish Medical.
Specifications
To give a broad overview of medical device adhesives, the following table provides context to parameters and the corresponding performance of adhesives.
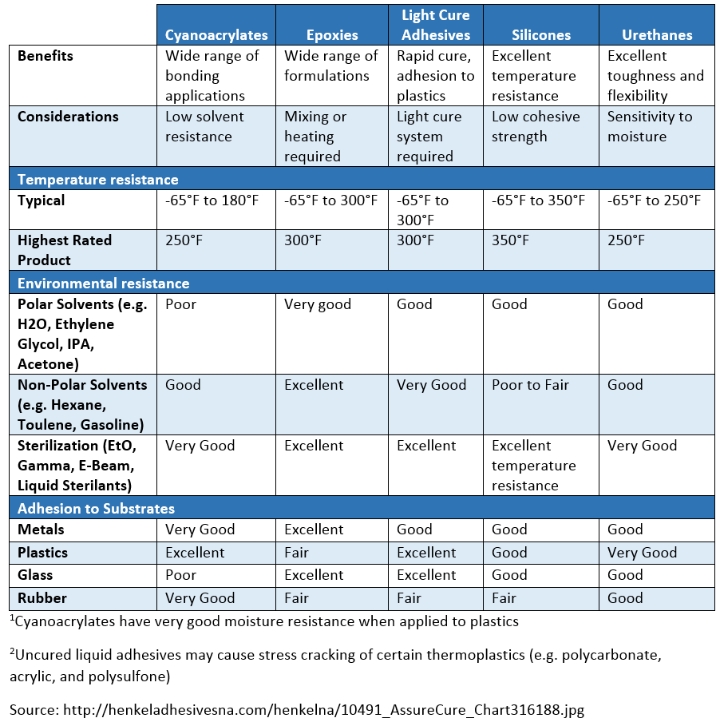
When choosing an adhesive, mechanical properties—along with chemical compatibility—are the fundamental factors to consider. Sound design practice, along with proper material and adhesive choices, will set the path towards successful design. Several failure modes and ways to circumvent them are outlined here in order to give clarity and lead to improved design using adhesives.
Failure Modes
In order to understand why adhesives fail, it is essential to acknowledge their mechanical modes of failure. There are three basic modes of failure, shown and explained below.
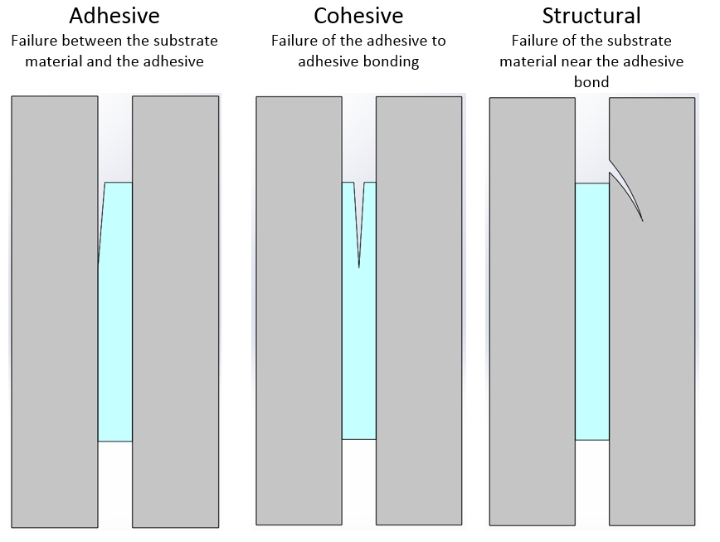
Adhesive failures are often due to a lack of surface preparation. This failure mode can be mitigated by several methods. Preparation of the substrate’s surface by using abrasives or bead/shot blasting to roughen will give better adhesion and bond strength. Cleanliness of the substrate is also of importance, due to the possibility of machining fluids, lubricants, and leftover materials (e.g., powder) causing adhesion issues. For most applications, degreasing with chemical methods—such as detergents and solvents—can lead to successful adhesion. For materials with lower surface energy, more specialized treatments (e.g., plasma or corona discharge) can enhance bondability.
Cohesive failure can be due to three key reasons. Higher thickness in bonds allows for more deformation in tension and shear, relying on the adhesives’ own strength between its internal bonds. As the thickness increases, the shear stresses increase, and therefore is more likely to lead to a cohesive failure. Mitigate this by following the adhesive’s directions closely, and by design of close fitting parts. Secondly, cohesive failure can be due insufficient bonding time or inadequate methods of curing (e.g., lack of full penetration of curing light). The final reason could simply be due to the maximum strength of the adhesive. Every adhesive will break at given stresses, and so careful planning for the application can allow for good results through a reliable bond. There are a number of factors that come together to create a properly cured adhesive. Following instructions from the adhesive’s manufacturer is key, as well as process control and verification testing, all of which can lead to consistent results for a bond.
Structural failure generally occurs due to stress concentrations created near a bonded joint. As with any material, there is an inherent yield and ultimate strength. Geometries and features of the component can amplify these effects, and lead to structural failure. Part analysis in software can reveal key flags during the design phase, leading to mitigations through design and allowing for an integral bond and part interface. In addition, chemical attack, particularly environmental stress cracking in plastics, can quickly cause structural failures in the base material.
Benefits of Adhesives over Fasteners
There are significant benefits of using adhesives over mechanical joining systems. This is dependent on the careful design and execution of the bonded joint. If well designed, adhesives can outshine mechanical bonding on several fronts.
Adhesives create a uniform and strong bond between materials by distributing stresses over an area. This reduces stress risers such as those that can occur with screws and rivets. Key to medical devices, adhesives do not require through holes, and can act simultaneously as both a sealant and a joining material. If an adhesive bond is designed as watertight, the area the adhesive covers will be protected from corrosion or liquid ingress. Space requirements are also an important consideration—adhesives can be used in place of fasteners when limited by the size of a joint or fastening region, as they are able to join materials with very limited additional volume. In some cases, a bonded assembly can be more durable than a fastened assembly due to vibration resistance, as adhesive will not loosen as with unsupported fasteners. Adhesives can save time and material cost during assembly, with the possibility of automation for high volumes. Automation, in certain cases, can be faster than with traditional fasteners, depending on the application. Also, depending on the adhesive selected, bonded assemblies can be disassembled through the application of adhesive removal compounds, allowing them to be disassembled alike to fastened assemblies.
Beyond function, the appearance of an assembly can be enhanced by adhesives, due to the absence of visible fasteners. From a risk mitigation standpoint, this also protects the user from device internals. Fasteners can be removed with tools, while most adhesives seal permanently and are arduous to separate.
Biocompatibility
A material is considered biocompatible if it lacks any negative interaction with living tissues or systems. Biocompatibility of a medical device that comes into human contact is of utmost importance, and should be top of mind during its development stage.
Merits of using adhesives over fasteners can also be applied to biocompatibility testing. By acting to seal parts together, adhesives limit the ingress of fluid into and between parts. This can reduce risk during testing due to less potential material contact (e.g., fluid contacts only external parts of device, thus excluding internals from the scope of biocompatibility testing).
As with all medical device testing, biocompatibility testing and validation is defined by the end use of the product and its component parts. The downselection for required testing involves defining a device category and the nature of bodily contact. Finally, the duration of contact defines further required testing. An important note is that the FDA only approves the final device, and not its component parts or materials. However, medical adhesive vendors can claim certain ISO 10993 or USP compliance by testing their cured adhesive, allowing designers to make the right adhesive choice for their device. These tests can clear a material for a particular application and provide confidence that the adhesive joints in an assembly will be non-toxic.
For further details on testing and requirements, consult biocompatibility standards ISO 10993 and USP series I to VI.
Applications
Adhesives can be categorized into the following segments:
- Structural: adhesives with defined load bearing properties, typically chemically curing, resulting in high strength bonds for the most demanding applications.
- Non-structural: adhesives for uses other than load bearing, typically physically curing (solvent/water evaporation, hot melt), for light-duty or cosmetic applications.
- Pressure Sensitive: adhesives generally for temporary applications, cured through the application of pressure between two surfaces, primary application—skin-based.
Understanding the application for a given adhesive and the bond’s mechanical property requirements are crucial to bond joint design. So too are the adhesive types recommended for each application. The table below provides examples of typical materials and applications for a range of structural, non-structural, and pressure sensitive adhesives.
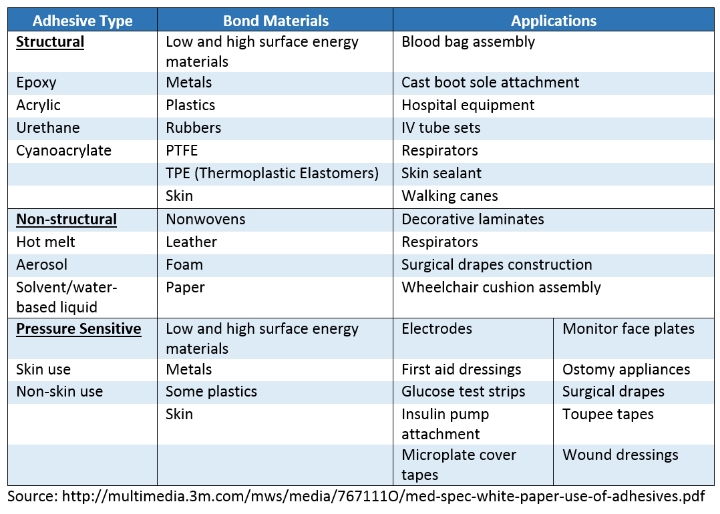
Conclusion
Medical devices require careful consideration when choosing adhesives. From design of the base part to the application method to the final intended use, many factors can affect the success of an adhesive joint. Prudent and conscious design choices are key factors in determining the success of any medical product.
Adhesives can offer many merits over designing with fasteners. They can provide cost reduction in many cases, and offer another choice to increase flexibility in design. They can be pre-tested by vendors to confirm their compliance with ISO 10993 or USP I to VI and be used to bond and seal between parts. These factors can assist in passing biocompatibility testing of the completed device. Overall, their applications are broad and their use in the medical field will only grow as both device variety and adhesive technologies advance in the years to come.
Nathan Müller, EIT, is a mechanical engineer at StarFish Medical.